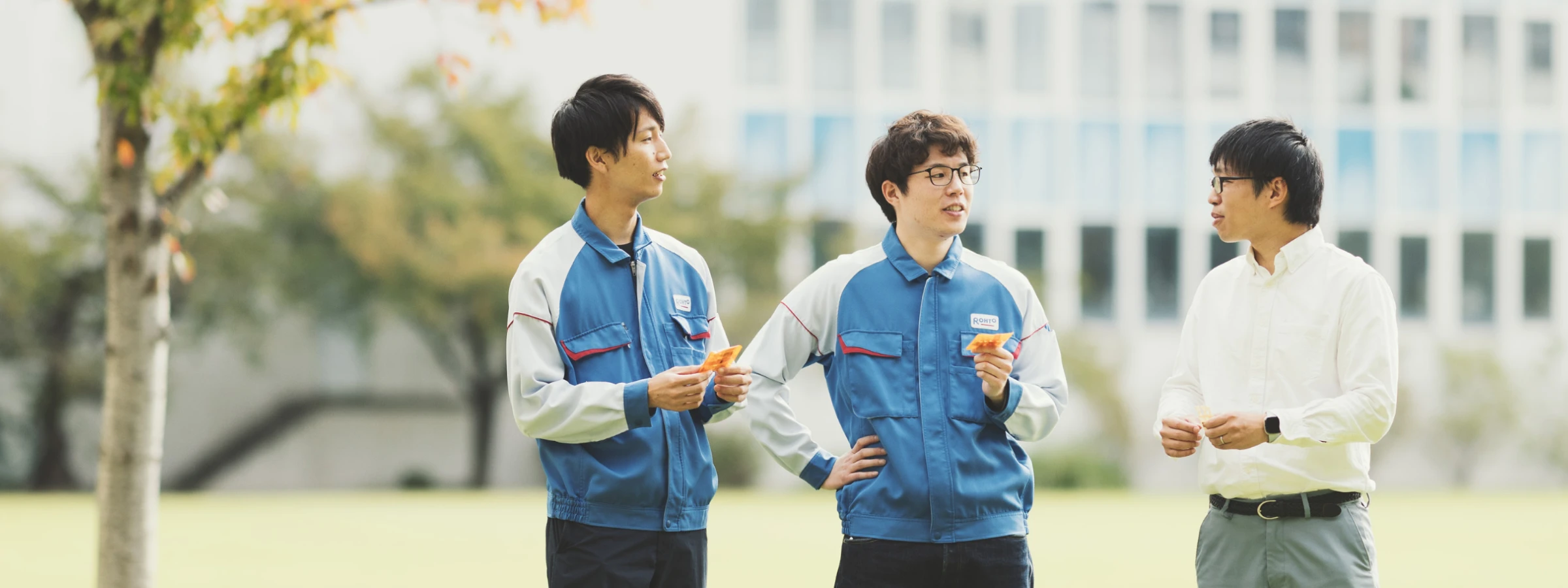
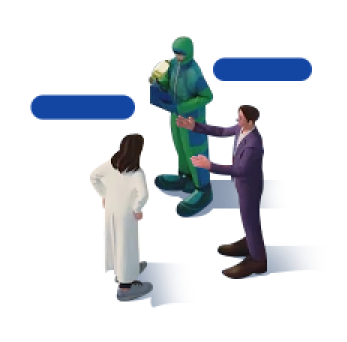
CROSS TALK - 02
ブローフィルシール製造導入プロジェクト
職種や部署を超えて行け。
新たな道は、領域外にこそある。
- プロジェクト概要
- ロート製薬の工場へ、新たに導入することとなったアイケア製品の製造方法「ブローフィルシール(BFS)」。国内外を意識し、メントールなどロートの強みを活かせる商品の製造ができると、導入前から大きな期待が寄せられていました。担当した社員たちは、プロジェクトの成功要因について「自分の担当ではない領域にも積極的だったから」と語ります。
-
プラントエンジニア
生産技術部けーちゃん
2013年新卒入社。生産技術としてBFSの設備導入を担当。品質マネジメント担当と連携し、新たな設備導入とアイケア製品ではマストとなる無菌条件の実現に注力した。
-
品質マネジメント
信頼性保証部(元品質統括部)たっきー
2016年新卒入社。新規設備導入にあたり、規制の遵守、そのための手段について検討。ロート製薬としての品質を守る、砦を担う。
-
ビジネス企画
国際事業部しょう
2012年新卒入社。主に海外向けの認可を担当。必要となるデータの取りまとめや提出書類の準備を、多方面と連携して行った。
Session - 01
まだどこもやってないメントール製品がある。
なら、ロートがやるしかないだろう。
- たっきー
-
まずこのプロジェクトを語るには、「ブローフィルシール(以下、BFS)」とは何か、これを読むみなさんに知ってもらう必要がありますよね。そこがわからないと、私たちが何に注力したのかも、このプロジェクトがいかにチャレンジングなのかも伝わらない。
- けーちゃん
-
個人的にも思い入れのあるプロジェクトなので、知ってほしいです!
- しょう
-
そもそも目薬などのアイケア商品の容器には、大きく2つの種類があります。蓋を開け閉めして何度も使える「マルチドーズ」と、1回分を切り分けて使い切る「ユニットドーズ」。後者のユニットドーズの製造方法としてあるのがBFSです。容器の成型・中身となる製剤の充填・容器の密封を同時に行う製造方法。元々ロートはこのBFSを自社工場では採用しておらず、外部の工場へ委託して製造していました。
- けーちゃん
-
新たに設備を導入し、自社工場で製造しようとしたのがこのプロジェクトというわけです。ただ、そもそもの目的は、ロートの得意とするメントールが入った目薬の、ユニットドーズ型のものをつくりたいということろから始まったのでしたね。当時はメントールが入ったユニットドーズ型の目薬は、他にありませんでした。むしろ、ないからこそ、我々がやろうと。
- しょう
-
ユニットドーズ型は海外での需要も見込めたので、やるしかないと考えていましたね。ちなみに、2023年現在でもメントールが入ったユニットドーズ型の目薬をつくっているのはロートだけです。
- たっきー
-
既存のユニットドーズ製造設備では容器にメントールが吸着し、メントール入りの製品を上手くつくれなかった。
- けーちゃん
-
新しい製造方法を開発し、それを実現する設備を自社工場へ導入することになりました。
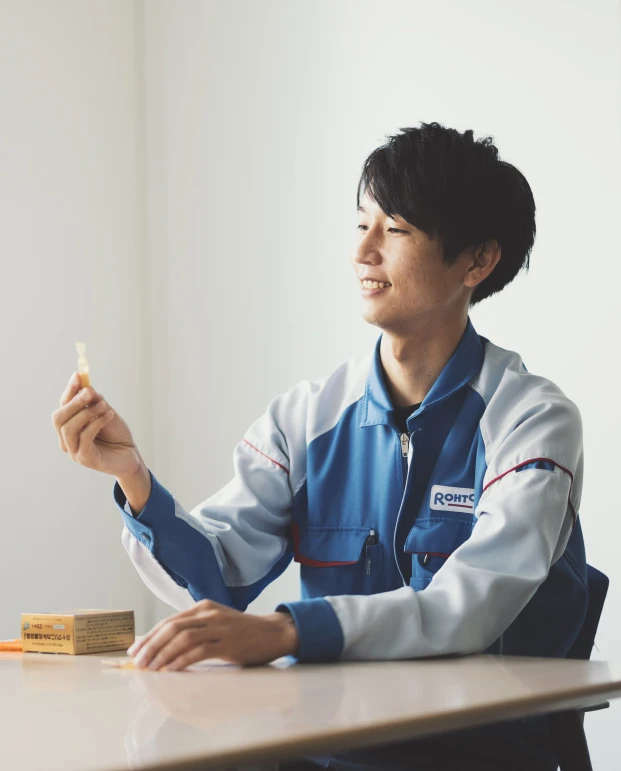
Session - 02
前例のなさを苦しみ、そして楽しめ。
- けーちゃん
-
設備の導入を担当したのは私です。そもそも新しい設備を導入するだけでも大変ですが、ロートにとって初めての設備なので参考になる技術文書が少なく、社内に経験のある人もいない状態。さらにはプロジェクト開始直後に世の中はコロナ禍となり、海外製の機械を導入したものの現地からのエンジニアは急遽帰国してしまい……。とにかく全てが初めてで手探りでした。
- たっきー
-
誰も答えを知らない点が、苦しくもあり面白くもあったプロジェクトでしたね。品質保証は、基本的にはその製造環境や設備が安全かどうか、規制に見合っているかをチェックします。しかし新しい設備で新しい製品をつくるとなると、どんな体制でどんな検査をすれば安全だと言えるのか、誰も知らないんですよね。
- しょう
-
私は製造環境や設備に関して書類を作成し、行政機関等へ申請。規制をクリアできるようにしました。やはり前例がない難しさは感じましたね。書類に何を記載するか、どんなデータを入れるか、ちょっとしたことで許可が降りない場合もあります。加えてグローバルを意識するなら、国によって規制が異なるため、それぞれに合わせる必要がありました。規制が厳しい国や審査に時間がかかる国は難易度が高いです。
- たっきー
-
規制は絶対に守るべきものですが、100%理想的な環境もそもそもあり得ません。だからどういうやり方ならできるか、何がわかれば安全を証明できるか、ある程度解釈する必要があります。そのためには現場の運用を知らなければならなかったので、生産技術のけーちゃんと常に相談しました。
- けーちゃん
-
自分の担当範囲だけを見ていてもダメなんですよね。私は設備のことだけでなく、品質の規制を知らないといけない。たっきーさんも設備のことを勉強したと思うし、しょうさんは現場から海外まで意識したと思います。
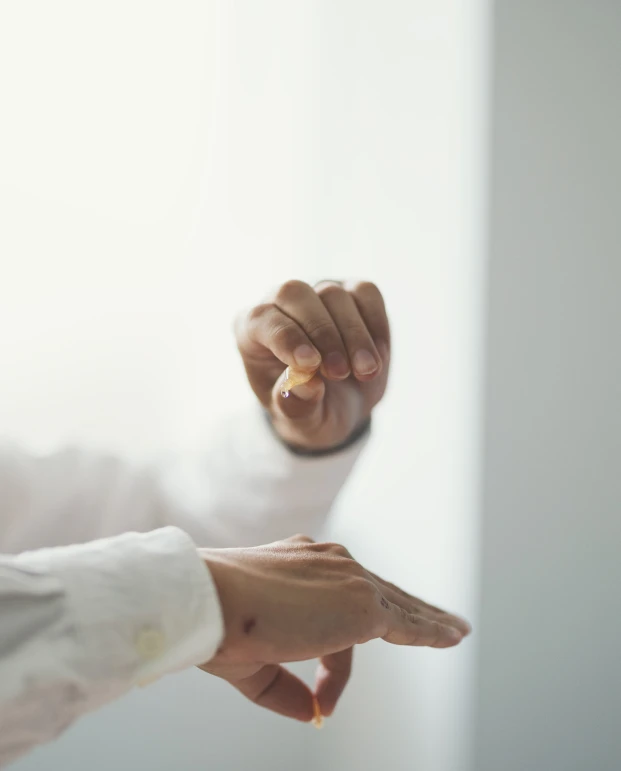
Session - 03
職種や担当にとらわれるな。
製品を世に届けることが全員のミッションだ。
- たっきー
-
みなさんから挙がったように、与えられた領域を超えて連携することは、今後も意識したい学びになりましたよね。
- しょう
-
はい。互いに自分の領域しか知らないと、「こうしてください」「できません」でコミュニケーションが終わってしまう。でも知識があると「こういうことがやりたいのですが」「こういう方法に変えればできるかも」と提案しながら道を探せると思います。
- けーちゃん
-
私は自分のことを、単なる設備エンジニアではなく、製薬会社の一員としてのエンジニアだと意識しています。つまりエンジニアとして与えられるものをこなすだけではダメで、製薬会社として製品を世に送り出すまでを考えるのがそもそもの仕事。おふたりも単なる品質管理、単なるビジネス企画、ではないことを意識されているんじゃないかな。
- たっきー
-
わかります。本来の仕事のスタイルであれば試験室やデスクでの仕事が中心になるのですが、このプロジェクトではとにかく現場へ行くことを心がけていました。
- けーちゃん
-
みんなでやる意識を持つからこそ実現できる製品があるし、きっとその方が楽しい。色んな人の力でいろんな価値を生み出していきたいですね。
- しょう
-
今回のプロジェクトによって、無菌環境やユニットドーズ、BFS、海外展開など、新しい知見がたくさん得られたと思います。これらはきっとこれからのロートに繋がっていくはず。いろんなことにアンテナを立てながら、「こうやったら面白いかな」「これなら実現できるかな」と前向きに考え続ける私たちでありたいです。
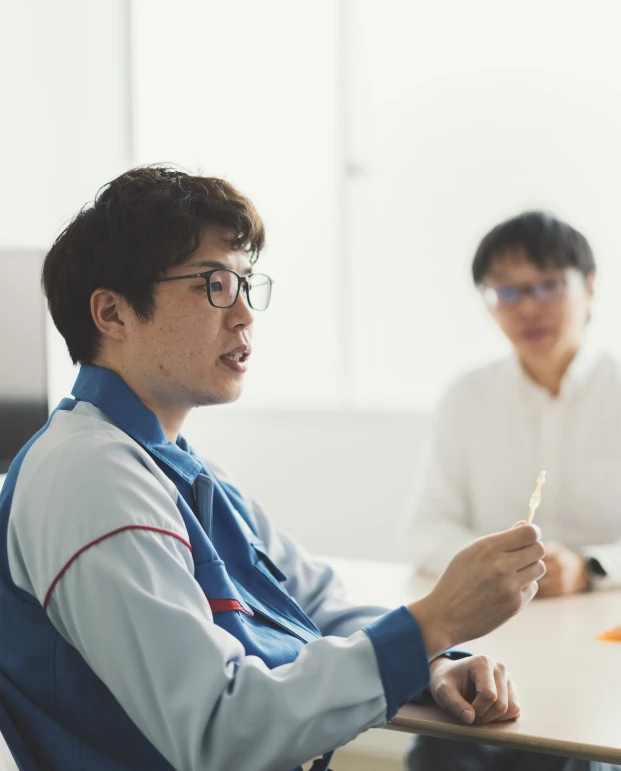
BACK TO INDEX
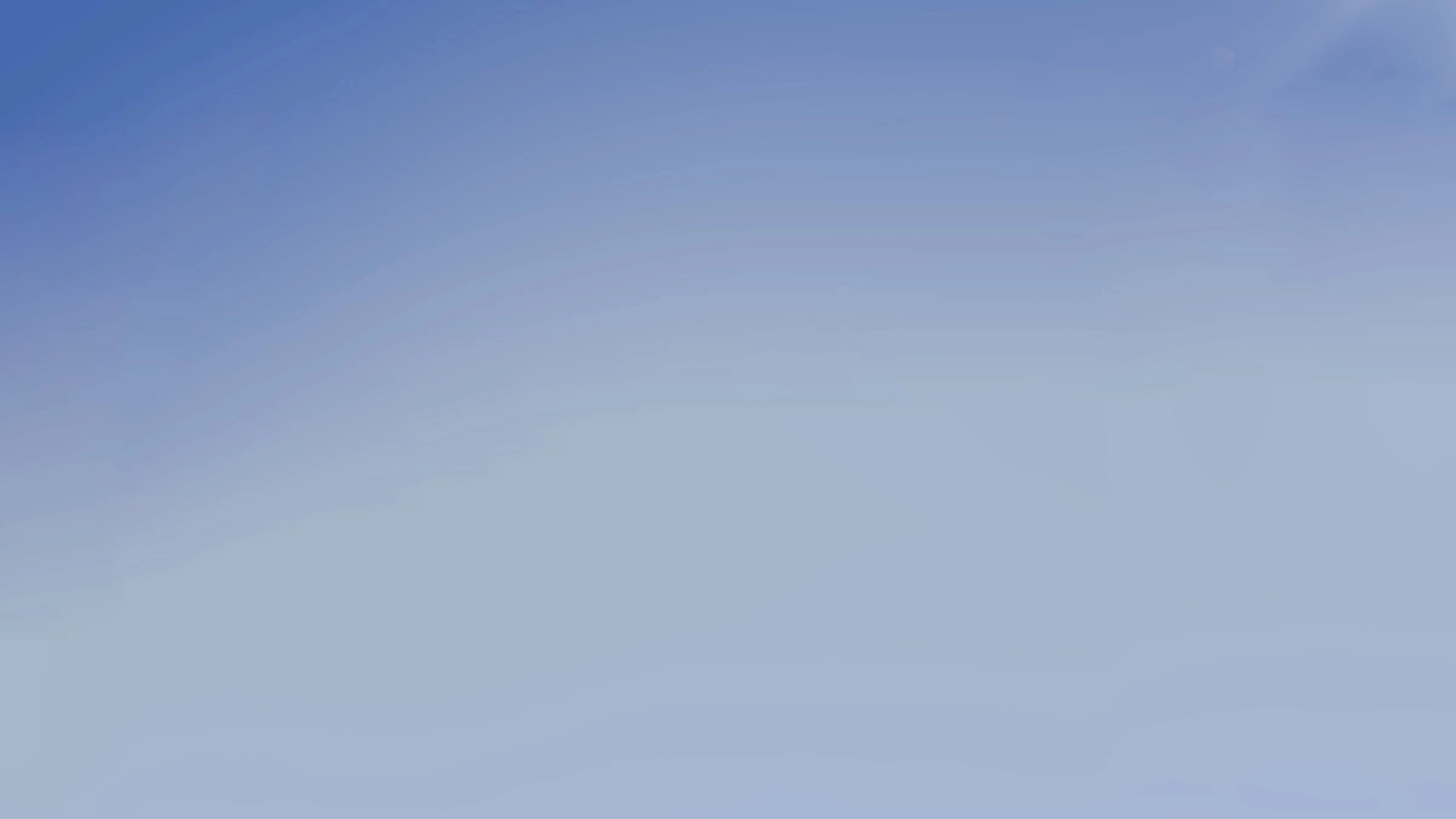
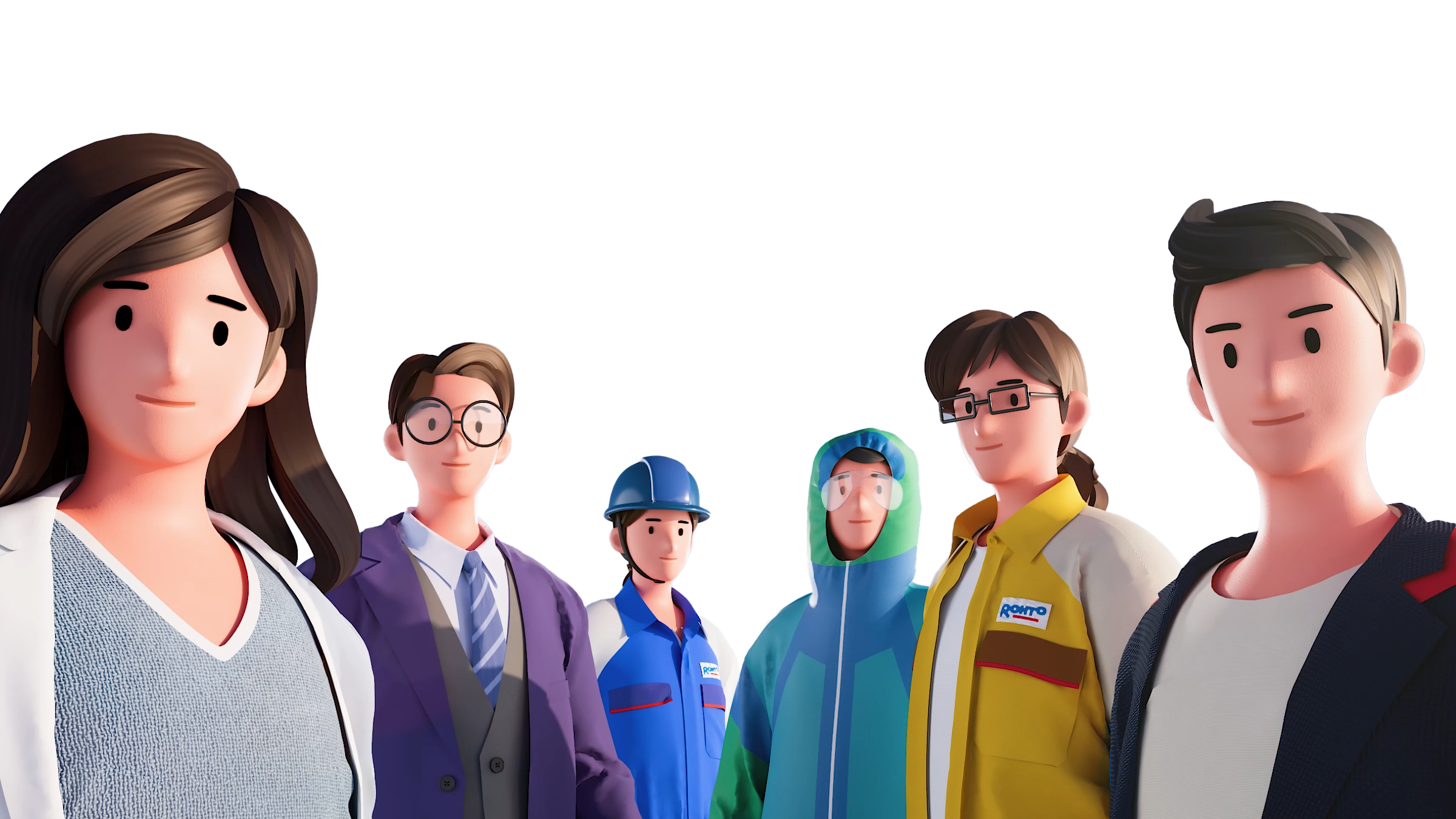